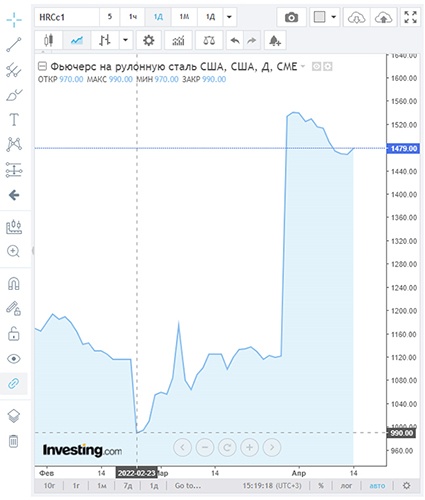
Сталь еще в цене
Кузовщики автомобилей все больше уходят от использования в них стали, заменяя ее в первую очередь гораздо более легким алюминием, а также синтетическими и углеродными волокнами. Несмотря на свои несомненные преимущества, эти комплектующие очень дороги, что, учитывая современные экономические требования, означает, что сталь еще долго будет использоваться в качестве базового компонента в конструкции кузовов автомобилей. В пользу этого вида материала говорит еще один факт: со сталью легко работать, отдельные элементы из этого материала также можно комбинировать различными способами.
Сталь = одни преимущества?
По крайней мере, так говорят специалисты, подчеркивая, что одним из важнейших является высокий модуль упругости и широкий диапазон прочности, в широких пределах от 70 до даже 1800 МПа. Сталь также характеризуется высокой прочностью на растяжение, до 320 МПа. Другими преимуществами являются низкая стоимость и универсальная доступность при одновременном высоком удобстве использования. Также важно сохранить хорошие свойства стали в области крупносерийного производства и ремонта отдельных элементов кузова автомобиля.
Худенький, худеющий
Основной предпосылкой использования алюминиевых или пластиковых компонентов является «похудение» тела, то есть уменьшение собственного веса. Между тем оказывается, что это можно сделать и из… традиционной стали. Уже широко используемые металлические листы толщиной 0,7 мм заменяются более тонкими в диапазоне от 0,5 до 0,4 мм. Вероятно, вскоре можно будет использовать еще более «утонченную» сталь, достигающую толщины кромки 0,34 мм. И без того хорошие параметры стали можно дополнительно увеличить путем ее прессования и закалки. Сам процесс прессования осуществляется при повышенной температуре до 960 градусов Цельсия, после чего сталь охлаждается или закаливается. В результате прочность отдельных листов может быть увеличена до 1700 МПа.
Сварные или клееные?
В случае современных кузовов автомобилей из качественной закаленной стали отдельные элементы соединяются не сваркой, а склейкой. Почему? Дело в том, что при традиционной сварке само место расположения шва не затвердевает, как и целые поверхности соединяемых между собой элементов, а потому не сохраняет такой твердости и эластичности. Поэтому лучше использовать метод склеивания, так как благодаря этому можно сохранить безопасный запас по различным линейным расширениям отдельных элементов кузова (в диапазоне температур от — 50 градусов С до даже +90 градусов С).
Когда необходима сварка
Однако оказывается, что даже в случае с самыми современными кузовными конструкциями не всегда можно использовать метод склеивания. Во многих случаях, кроме сварки и упомянутой выше склейки, необходимо соединение отдельных элементов сваркой. В таких случаях в зависимости от толщины соединяемых листов выбираются токово-временные параметры сварочного аппарата. Кроме того, в самых современных типах сварочных аппаратов используется т.н. динамическое регулирование процесса. О чем это? Благодаря датчикам, размещенным в сварочном пистолете, измеряются толщина отдельных листов и сварочное напряжение. Это происходит как перед началом самого процесса сварки, так и во время него. Это обеспечивает выполнение соответствующего сварного шва без чрезмерного и нежелательного нагрева поверхности листов в местах их соприкосновения, что могло бы ослабить их структуру и снизить эластичность.

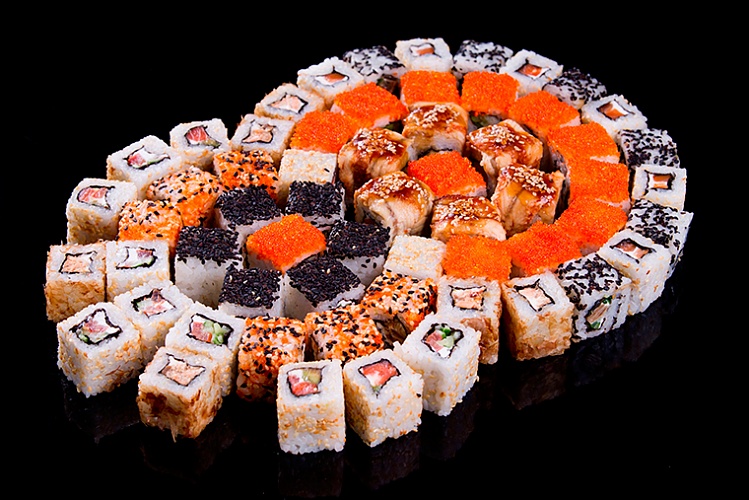