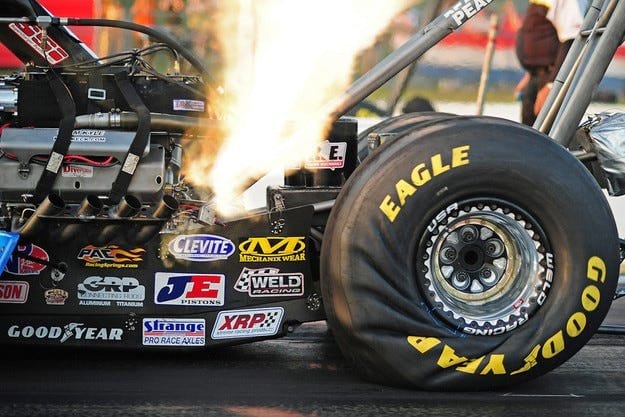
Тест драйв Magic Fires: история компрессорной техники
В серии мы расскажем о принудительной заправке и развитии двигателей внутреннего сгорания.
Он — пророк в писаниях тюнинга автомобилей. Он спаситель дизельного двигателя. Многие годы конструкторы бензиновых двигателей пренебрегали этим явлением, а сегодня он становится повсеместным. Это турбокомпрессор… Более совершенный, чем когда-либо.
Его брат, компрессор с механическим приводом, тоже не планирует уходить со сцены. Более того, он готов к союзу, который приведет к идеальному симбиозу. Таким образом, в суматохе современного технологического соперничества представители двух доисторических противостоящих течений объединились, доказав максиму, согласно которой истина остается неизменной независимо от разницы во взглядах.
Расход 4500 л / 100 км и много кислорода
Арифметика относительно проста и основана исключительно на законах физики… Предполагая, что автомобиль весом около 1000 кг и безнадежным аэродинамическим сопротивлением преодолевает 305 метров с места менее чем за 4,0 секунды, достигая в конце скорости 500 км / ч. на участке мощность двигателя этого автомобиля должна превышать 9000 л.с. Те же расчеты показывают, что внутри сечения вращающийся коленчатый вал двигателя, вращающегося со скоростью 8400 об / мин, сможет повернуться всего около 560 раз, но это не помешает 8,2-литровому двигателю поглотить около 15 литров топлива. В результате еще одного несложного расчета становится ясно, что по стандартной мере расхода топлива средний расход этого автомобиля составляет более 4500 л / 100 км. Одним словом — четыре тысячи пятьсот литров. На самом деле у этих двигателей нет систем охлаждения — они охлаждаются топливом …
В этих цифрах нет ничего вымысла… Это большие, но вполне реальные ценности из мира современного дрэг-рейсинга. Относить машины, участвующие в гонках по максимальному разгону, к гоночным машинам вряд ли будет правильно, так как сюрреалистические четырехколесные создания, окутанные голубым дымом, несравнимы даже со сливками современных автомобильных технологий, используемых в Формуле 1. Поэтому мы будем использовать популярное название «драгстеры». — Несомненно интересные по-своему, неповторимые автомобили, доставляющие неповторимые ощущения как болельщикам за пределами 305-метровой трассы, так и пилотам, мозг которых при быстром ускорении в 5 g, вероятно, принимает вид цветного двухмерного изображения на задней стенке черепа черепа
Эти драгстеры, пожалуй, самая известная и самая впечатляющая разновидность популярного автоспорта в США, принадлежащая к классу с неоднозначным названием Top Fuel. Название основано на экстремальных характеристиках химического соединения нитрометана, который адские машины используют в качестве топлива для своих двигателей. Под воздействием этой взрывоопасной смеси двигатели работают в режиме перегрузки и всего за несколько гонок превращаются в груду ненужного металла, а из-за склонности топлива к непрерывной детонации звук их работы напоминает истерический рев зверя, считающего последние моменты вашей жизни. Процессы в двигателях можно сравнить только с абсолютным неуправляемым хаосом, граничащим с погоней за физическим самоуничтожением. Обычно к концу первой секции выходит из строя один из цилиндров. Мощность двигателей, используемых в этом безумном спорте, достигает значений, которые не может измерить ни один динамометр в мире, а злоупотребление машинами действительно превышает все пределы инженерного экстремизма …
Но давайте вернемся к сути нашей истории и подробнее рассмотрим свойства нитрометанового топлива (смешанного с несколькими процентами уравновешивающего метанола), который, без сомнения, является самым мощным веществом, используемым в любой форме автомобильных гонок. деятельность. Каждый атом углерода в своей молекуле (CH3NO2) имеет два атома кислорода, а это означает, что топливо несет с собой большую часть окислителя, необходимого для сгорания. По той же причине содержание энергии на литр нитрометана ниже, чем на литр бензина, но с тем же количеством свежего воздуха, которое двигатель может всасывать в камеры сгорания, при сгорании нитрометан будет обеспечивать значительно большее общее количество энергии. . Это возможно, потому что он сам содержит кислород и поэтому может окислять большинство углеводородных компонентов топлива (обычно негорючих в отсутствие кислорода). Другими словами, нитрометан имеет в 3,7 раза меньше энергии, чем бензин, но при том же количестве воздуха можно окислить в 8,6 раза больше нитрометана, чем бензин.
Любой, кто знаком с процессами сгорания в автомобильном двигателе, знает, что настоящая проблема с «выжатием» большей мощности из двигателя внутреннего сгорания заключается не в увеличении потока топлива, поступающего в камеры — для этого достаточно мощных гидравлических насосов. достижение чрезвычайно высокого давления. Действительно сложная задача — обеспечить достаточно воздуха (или кислорода) для окисления углеводородов и обеспечения максимально эффективного сгорания. Именно поэтому в топливе драгстеров используется нитрогетан, без которого было бы совершенно немыслимо добиться результатов такого порядка с двигателем рабочим объемом 8,2 литра. При этом машины работают с довольно богатыми смесями (при определенных условиях нитрометан может начать окисляться), из-за чего часть топлива окисляется в выхлопных трубах и образует над ними впечатляющие магические огни.
Крутящий момент 6750 ньютон-метров
Средний крутящий момент этих двигателей достигает 6750 Нм. Вы, наверное, уже заметили, что во всей этой арифметике есть что-то странное … Дело в том, что для достижения указанных предельных значений каждую секунду двигатель, работающий при 8400 об / мин, должен всасывать не больше, не менее 1,7 XNUMX кубометров свежего воздуха. Есть только один способ сделать это — принудительное заполнение. Основную роль в этом случае выполняет огромный классический механический агрегат типа Рутс, благодаря которому давление в коллекторах двигателя драгстера (по мотивам доисторических Chrysler Hemi Elephant) достигает ошеломляющих 5 бар.
Чтобы лучше понять, какие нагрузки задействованы в этом случае, приведем в качестве примера одну из легенд золотого века механических компрессоров — 3,0-литровый гоночный V12. Mercedes-Benz W154. Мощность этой машины составляла 468 л.с. с., но при этом следует учитывать, что привод компрессора брал колоссальные 150 л.с. с., не достигнув указанных 5 бар. Если теперь добавить к счету 150 тыс. с., мы придем к выводу, что W154 действительно имел невероятные для своего времени 618 л.с. Вы можете сами судить, какой реальной мощности достигают двигатели в классе Top Fuel и какая ее часть поглощается приводом механического компрессора. Конечно, использование турбокомпрессора в этом случае было бы намного эффективнее, но его конструкция не могла справиться с экстремальной тепловой нагрузкой от выхлопных газов.
Начало сокращения
На протяжении большей части истории автомобиля наличие блока принудительного зажигания в двигателях внутреннего сгорания было отражением новейших технологий для соответствующей стадии разработки. Так было в 2005 году, когда престижная награда за технологические инновации в автомобильной индустрии и спорте, названная в честь основателя журнала Пола Пича, была вручена главе отдела разработки двигателей VW Рудольфу Кребсу и его команде разработчиков. применение технологии Twincharger в 1,4-литровом бензиновом двигателе. Благодаря комбинированному принудительному наполнению цилиндров с помощью синхронной системы механики и турбонагнетателя, в агрегате умело сочетаются равномерное распределение крутящего момента и высокая мощность, характерные для атмосферных двигателей с большим рабочим объемом, с экономичностью и экономичностью малых двигателей. Одиннадцать лет спустя 11-литровый двигатель TSI VW (с немного увеличенным рабочим объемом, чтобы компенсировать его эффективное сокращение из-за используемого цикла Миллера) теперь оснащен гораздо более совершенной технологией турбокомпрессора VNT и снова номинирован на премию Paul Peach Award.
Фактически, первый серийный автомобиль с бензиновым двигателем и турбонаддувом с изменяемой геометрией, Porsche 911 Turbo увидел свет в 2005 году. Оба компрессора, разработанные совместно инженерами Porsche R&D и их коллегами из Borg Warner Turbo Systems, VW используют хорошо известную и давно устоявшуюся идею переменной геометрии в турбодизельных агрегатах, которая не была реализована в бензиновых двигателях из-за проблемы с более высокой (примерно на 200 градусов по сравнению с дизелем) средней температурой выхлопных газов. Для этого были использованы термостойкие композитные материалы из аэрокосмической промышленности для газовых направляющих лопаток и сверхбыстрого алгоритма управления в системе управления. Достижение инженеров VW.
Золотой век турбокомпрессора
После снятия с производства 745i в 1986 г. BMW долгое время они твердо отстаивали собственную конструктивную философию при создании бензиновых двигателей, согласно которой единственным «ортодоксальным» способом достижения большей мощности была работа двигателя на высоких оборотах. Никаких ересей и заигрываний с механическими компрессорами а-ля Мерседес (C 200 Kompressor) или Toyota (Компрессор Corolla), без уклона в сторону VW или турбокомпрессоров с турбонаддувом Opel. Мюнхенские двигателестроители отдавали предпочтение высокочастотному наполнению и нормальному атмосферному давлению, применению высокотехнологичных решений и, в крайнем случае, большему рабочему объему. Компрессорные эксперименты на базе баварских двигателей почти полностью были переданы «факирам» тюнинговой компанией Alpina, близкой к мюнхенскому концерну.
Сегодня BMW больше не производит бензиновые двигатели без наддува, а в линейку дизельных двигателей уже входит четырехцилиндровый двигатель с турбонаддувом. Volvo использует комбинацию заправки с механическим и турбонагнетателем, Audi создал дизельный двигатель с комбинацией электрического компрессора и двух каскадных турбонагнетателей, Mercedes — бензиновый двигатель с электрическим и турбонагнетателем.
Однако, прежде чем говорить о них, мы вернемся в прошлое, чтобы найти корни этого технологического перехода. Мы узнаем, как в восьмидесятые годы американские производители пытались с помощью турботехнологий компенсировать снижение объемов двигателя в результате двух нефтяных кризисов и как они потерпели неудачу в этих попытках. Мы расскажем о безуспешных попытках Рудольфа Дизеля создать компрессорный двигатель. Мы будем вспоминать славную эпоху компрессорных двигателей 20-30-х годов, а также долгие годы забвения. Конечно, мы не пропустим появление первых серийных моделей турбокомпрессоров после первого крупного нефтяного кризиса 70-х годов. Или для составной системы Scania Turbo. Вкратце — мы расскажем вам об истории и эволюции компрессорных технологий…
(следовать)
Текст: Георгий Колев
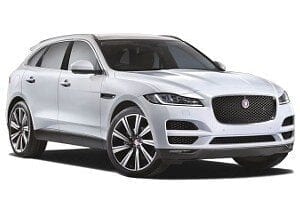
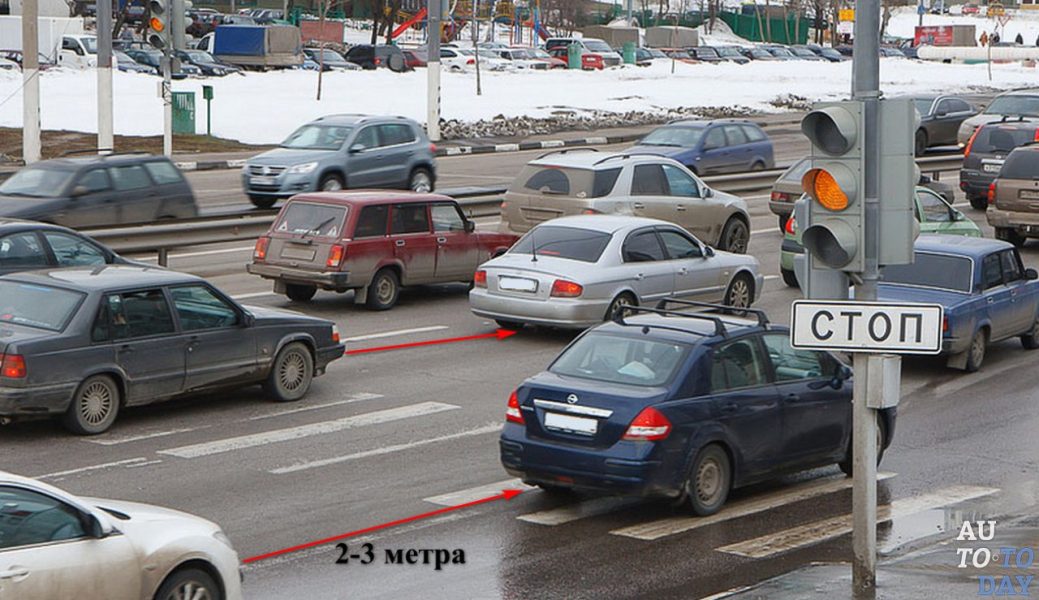