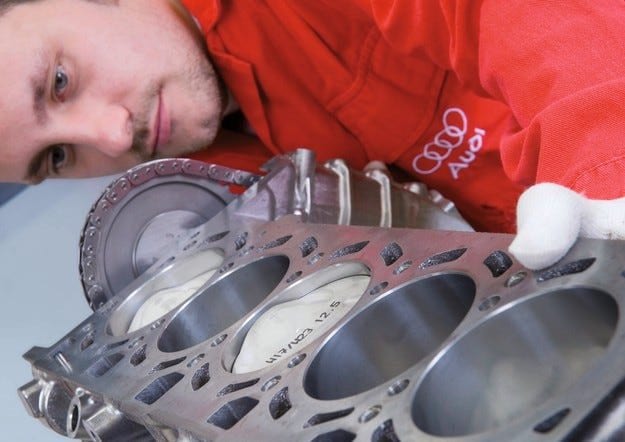
Тест драйв линейка двигателей Audi — Часть 1: 1.8 TFSI
Ассортимент приводных устройств марки — это воплощение невероятно высокотехнологичных решений.
Серия про самые интересные машины компании
Если мы ищем пример дальновидной экономической стратегии, обеспечивающей устойчивое развитие компании, то Audi может быть отличным примером в этом отношении. Вряд ли в 70-е годы кто-то мог предположить тот факт, что в настоящее время компания из Ингольштадта будет равным конкурентом такому устоявшемуся имени, как Mercedes-Benz. Ответ на причины во многом можно найти в слогане бренда «Прогресс через технологии», который является основой успешно пройденного сложного пути в премиальный сегмент. Область, где никто не имеет права идти на компромиссы и предлагает только лучшее. То, что могут сделать Audi и только несколько других компаний, гарантирует им спрос на их продукцию и достижение аналогичных параметров, но также является огромным бременем, требующим постоянного движения на острие технологической бритвы.
Являясь частью VW Group, Audi имеет возможность в полной мере использовать возможности развития огромной компании. Какие бы проблемы ни были у VW, с его ежегодными расходами на НИОКР почти 10 миллиардов евро, группа возглавляет список из 50 компаний с самыми высокими инвестициями в этой области, опережая таких гигантов, как Samsung Electronics, Microsoft, Intel и Toyota (где эта стоимость составляет чуть более 7 миллиардов евро). Сама по себе компания Audi по этим параметрам близка к BMWс их инвестициями в 4,0 миллиарда евро. Однако часть вложенных в Audi средств идет косвенно из общей казны концерна VW, так как разработки также используются другими брендами. Среди основных направлений этой деятельности — технологии производства легких конструкций, электроники, трансмиссий и, конечно же, приводов. И вот мы подошли к сути этого материала, который является частью нашей серии, представляющей современные решения в области двигателей внутреннего сгорания. Тем не менее, как элитное подразделение VW, Audi также разрабатывает конкретную линейку силовых агрегатов, предназначенных в первую очередь или только для автомобилей Audi, и мы расскажем вам о них здесь.
1.8 TFSI: образец высоких технологий во всех отношениях
История Audi рядных четырехцилиндровых двигателей TFSI восходит к середине 2004 года, когда первый в мире бензиновый турбокомпрессор EA113 с прямым впрыском увидел свет в виде 2.0 TFSI. Спустя два года появилась более мощная версия Audi S3. Разработка модульной концепции EA888 с приводом распредвала с цепью практически началась в 2003 году, незадолго до появления EA113 с ремнем ГРМ.
Однако EA888 был создан с нуля как глобальный двигатель VW Group. Первое поколение было представлено в 2007 году (в виде 1.8 TFSI и 2.0 TFSI); с введением системы изменения фаз газораспределения Audi Valvelift и рядом мер по снижению внутреннего трения в 2009 году было отмечено второе поколение, а в конце 2011 года последовало третье поколение (1.8 TFSI и 2.0 TFSI). Четырехцилиндровые двигатели серий EA113 и EA888 достигли для Audi невероятного успеха, получив в общей сложности десять престижных наград International Engine of the Year и 10 Best Engines. Задача инженеров — создать модульный двигатель рабочим объемом 1,8 и 2,0 литра, адаптированный как для поперечной, так и для продольной установки, со значительно сниженным внутренним трением и выбросами, отвечающий новым требованиям, в том числе Euro 6, с улучшенными характеристиками. выносливость и уменьшенный вес. На основе EA888 Generation 3 был создан и представлен в прошлом году EA888 Generation 3B, работающий по принципу, аналогичному принципу Миллера. Об этом мы расскажем позже.
Все это звучит хорошо, но, как мы увидим, для его достижения требуется много работы по развитию. Благодаря увеличению крутящего момента с 250 до 320 Нм по сравнению с предшественником в версии с рабочим объемом 1,8 литра, конструкторы теперь могут изменять передаточные числа на более длинные, что также снижает расход топлива. Огромный вклад в последнее — важное технологическое решение, которое затем использовалось рядом других компаний. Это интегрированные в головку выхлопные трубы, которые обеспечивают возможность более быстрого достижения рабочей температуры и охлаждения газов при высокой нагрузке и позволяют избежать необходимости обогащения смеси. Такое решение чрезвычайно рационально, но также очень сложно реализовать, учитывая огромную разницу температур между жидкостями по обе стороны коллекторных труб. Однако преимущества также включают возможность более компактной конструкции, которая, помимо снижения веса, гарантирует более короткий и оптимальный путь газов к турбине и более компактный модуль для принудительного заполнения и охлаждения сжатого воздуха. Теоретически это тоже звучит оригинально, но практическая реализация — настоящий вызов для профессионалов кастинга. Для отливки сложной головки блока цилиндров они создают особый процесс с использованием до 12 металлургических сердец.
Гибкое управление охлаждением
Еще один важный фактор снижения расхода топлива связан с процессом достижения рабочей температуры охлаждающей жидкости. Интеллектуальная система управления последнего позволяет полностью прекратить его циркуляцию до тех пор, пока он не достигнет рабочей температуры, и когда это происходит, температура постоянно контролируется в зависимости от нагрузки двигателя. Огромной проблемой было проектирование зоны, в которой охлаждающая жидкость заливает выхлопные трубы, где имеется значительный температурный градиент. Для этого была разработана комплексная аналитическая компьютерная модель, включающая общий состав газа / алюминия / теплоносителя. Из-за специфики сильного локального нагрева жидкости в этой области и общей потребности в оптимальном контроле температуры используется полимерный модуль управления ротором, который заменяет традиционный термостат. Таким образом, на этапе нагрева полностью перекрывается циркуляция теплоносителя.
Все внешние клапаны закрыты, и вода в рубашке замерзает. Даже если кабину нужно отапливать в холодную погоду, циркуляция не активируется, а используется специальный контур с дополнительным электронасосом, в котором поток циркулирует вокруг выпускных коллекторов. Такое решение позволяет намного быстрее обеспечить комфортную температуру в салоне, при оптимальном сохранении возможности быстрого прогрева двигателя. При открытии соответствующего клапана начинается интенсивная циркуляция жидкости в двигателе — так быстро достигается рабочая температура масла, после чего открывается клапан его охладителя. Температура охлаждающей жидкости контролируется в реальном времени в зависимости от нагрузки и скорости в диапазоне от 85 до 107 градусов (самый высокий при низкой скорости и нагрузке) во имя баланса между снижением трения и предотвращением детонации. И это еще не все — даже при выключенном двигателе специальный электронасос продолжает циркуляцию охлаждающей жидкости через чувствительную к кипению рубашку в головке и турбонагнетатель для более быстрого отвода тепла от них. Последнее не влияет на топы рубашек, чтобы избежать их быстрого переохлаждения.
Две форсунки на цилиндр
Специально для этого двигателя, чтобы достичь уровня выбросов Евро 6, Audi впервые внедряет систему впрыска с двумя форсунками на каждый цилиндр — одно для прямого впрыска, а другое — во впускной коллектор. Возможность гибкого управления впрыском в любое время приводит к более оптимальному смешиванию топлива и воздуха и снижает выбросы твердых частиц. Давление в секции прямого впрыска увеличено со 150 до 200 бар. Когда последний не работает, циркуляция топлива также обеспечивается байпасными соединениями через форсунки во впускных коллекторах для охлаждения насоса высокого давления.
При запуске двигателя смесь забирается системой непосредственного впрыска, а для обеспечения быстрого нагрева катализатора выполняется двойной впрыск. Эта стратегия обеспечивает лучшее перемешивание при низких температурах без заливания топливом холодных металлических частей двигателя. То же самое происходит с тяжелыми грузами, чтобы избежать детонации. Благодаря системе охлаждения выпускных коллекторов и его компактной конструкции стало возможным использование одноструйного турбонагнетателя (RHF4 от IHI) с размещенным перед ним лямбда-зондом и корпусом из более дешевых материалов.
В результате максимальный крутящий момент 320 Нм достигается при 1400 об / мин. Еще более интересным является распределение мощности с максимальным значением 160 л.с. доступен при 3800 об / мин (!) и остается на этом уровне до 6200 об / мин со значительным потенциалом для дальнейшего увеличения (таким образом устанавливая различные версии 2.0 TFSI, что увеличивает уровень крутящий момент в высоких диапазонах оборотов). Таким образом, увеличение мощности по сравнению с предшественником (на 12 процентов) сопровождается снижением расхода топлива (на 22 процента).
(следовать)
Текст: Георгий Колев
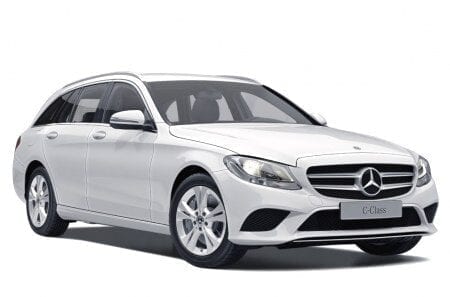
