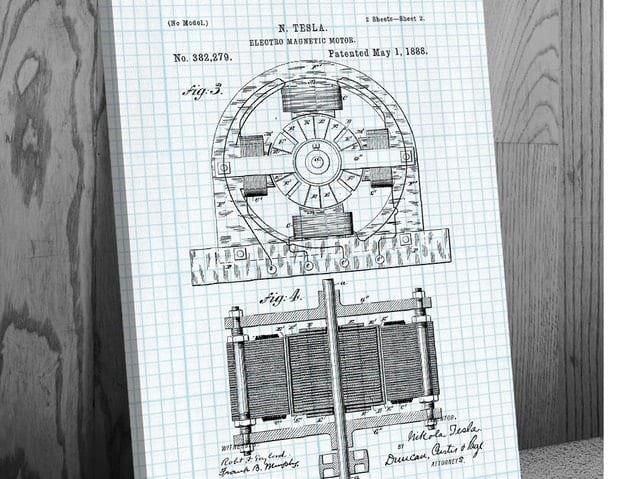
Nicola Tesla Electric Machine
Content
Electric motors are much more efficient than internal combustion engines. Why and when
The basic truth is that the problems of electric vehicles are related to the energy source, but they can be viewed from a different perspective. Like many things in life that we take for granted, the electric motor and control system in electric vehicles are considered the most efficient and reliable device in these vehicles. However, in order to achieve this state of affairs, they have come a long way in evolution - from discovering the connection between electricity and magnetism to its effective transformation into a mechanical force. This topic is often underestimated in the context of talking about the technological development of the internal combustion engine, but it is becoming increasingly necessary to talk more about the machine called the electric motor.
One or two motors
If you look at the performance graph of an electric motor, regardless of its type, you will notice that it is over 85 percent efficient, often over 90 percent, and that it is at its most efficient at around 75 percent load. maximum. As the power and size of the electric motor increase, the range of efficiency expands accordingly, where it can reach its maximum even earlier - sometimes at 20 percent load. However, there is another side to the coin - despite the extended range of higher efficiency, the use of very powerful motors with very low load can again lead to frequent entry into the low efficiency zone. Therefore, decisions regarding the size, power, number (one or two) and use (one or two depending on the load) of electric motors are processes that are part of the design work in the construction of a car. In this context, it is understandable why it is better to have two motors instead of a very powerful one, namely so that it does not often enter areas of low efficiency, and because of the possibility of shutting it down at low loads. Therefore, at partial load, for example, in the Tesla Model 3 Performance, only the rear engine is used. In less powerful versions, it is the only one, and in more dynamic versions, the asynchronous one is connected to the front axle. This is another advantage of electric vehicles - power can be increased more easily, modes are used depending on efficiency requirements, and dual powertrains are a useful side effect. However, the lower efficiency at low load does not prevent the fact that, unlike an internal combustion engine, an electric motor generates thrust at zero speed due to its fundamentally different principle of operation and interaction between magnetic fields even under such conditions. The aforementioned fact of efficiency is at the heart of the engine design and operating modes - as we have said, an oversized engine continuously running at low load would be inefficient.
With the rapid development of electric mobility, the diversity in terms of motor production is expanding. More and more agreements and arrangements are being developed, whereby some manufacturers such as BMW and VW design and manufacture their own cars, others buy shares in companies related to this business, and still others outsource to suppliers such as Bosch. In most cases, if you read the specifications of an electrically powered model, you will find that its motor is "AC permanent magnet synchronous". However, the Tesla pioneer uses other solutions in this direction - asynchronous motors in all previous models and a combination of asynchronous and so-called. “Resistance switching motor as rear axle drive in the 3 Performance model. In cheaper versions with rear-wheel drive only, it is the only one. Audi is also using induction motors for the q-tron model and a combination of synchronous and asynchronous motors for the forthcoming e-tron Q4. What is it really about?
Nicola Tesla Electric Machine
The fact that Nikola Tesla invented the asynchronous or, in other words, the "asynchronous" electric motor (back in the late 19th century) has no direct connection to the fact that Tesla Motors models are one of the few cars powered by such a machine. ... In fact, the operating principle of the Tesla motor became more popular in the 60s, when semiconductor devices were gradually emerging under the sun, and American engineer Alan Coconi developed portable semiconductor inverters that can convert direct current (DC) batteries into alternating current (AC) as required for an induction motor, and vice versa (in the process of recovery). This combination of an inverter (also known as an engineering transverter) and an electric motor developed by Coconi became the basis for the infamous GM EV1 and, in a more refined form, the sporty tZERO. By analogy with the search for Japanese engineers from Toyota during the creation of the Prius and the discovery of the TRW patent, the creators of Tesla discovered the tZERO car. Eventually, they bought a tZero license and used it to build a roadster.
The biggest advantage of an induction motor is that it does not use permanent magnets and does not need expensive or rare metals, which are also often mined under conditions that create moral dilemmas for consumers. However, both asynchronous and permanent magnet synchronous motors make full use of technological advances in semiconductor devices, as well as in the creation of MOSFETs with a field effect transistor and later transistors with bipolar isolation (IGBT). It is this progress that allows us to create the mentioned compact inverter devices and, in general, all power electronics in electric vehicles. The fact that the ability to efficiently convert DC batteries to three-phase variables and vice versa is largely due to advances in control technology may seem trivial, but keep in mind that the current in power electronics reaches levels many times higher than usual in household electrical network, and often values exceed 150 amperes. This generates a large amount of heat that power electronics must deal with.
But back to the issue of electric motors. Like internal combustion engines, they can be divided into various qualification parameters, and “synchronization” is one of them. In fact, this is a consequence of a much more important other constructive approach in terms of the generation and interaction of magnetic fields. Despite the fact that the source of electricity in the face of the battery is direct current, the designers of electrical systems do not even think about using DC motors. Even taking into account conversion losses, AC units and especially synchronous units win competition with DC elements. So what does a synchronous or asynchronous motor really mean?
Auto Motor Company
Both synchronous and asynchronous motors belong to the type of electric machines with a rotating magnetic field, which have a higher power density. In general, an asynchronous rotor consists of a simple package of solid sheets, metal rods of aluminum or copper (more and more often used recently) with coils in a closed loop. The current flows in the stator windings in opposite pairs, and the current from one of the three phases flows in each pair. Since in each of them it is phase shifted by 120 degrees relative to the other, the so-called rotating magnetic field. The intersection of the rotor windings with the magnetic field lines from the field created by the stator leads to the flow of current in the rotor, similar to the interaction on the transformer.
The resulting magnetic field interacts with the "rotating" in the stator, which leads to mechanical capture of the rotor and subsequent rotation. However, with this type of electric motor, the rotor always lags behind the field, because if there is no relative motion between the field and the rotor, the magnetic field will not be induced in the rotor. Thus, the maximum speed level is determined by the frequency of the supply current and the load. However, due to the higher efficiency of synchronous motors, most manufacturers adhere to them, but for some of the above reasons, Tesla remains a supporter of asynchronous.
Yes, these machines are cheaper, but they do have their downsides, and all the people who have tested multiple successive accelerations with the Model S will tell you how performance drops off drastically with each iteration. The processes of induction and the flow of current lead to heating, and when the machine is not cooled under high load, heat accumulates and its capabilities are significantly reduced. For protection purposes, the electronics reduce the amount of current and the acceleration performance is degraded. And one more thing - to be used as a generator, the induction motor must be magnetized - that is, to "pass" the initial current through the stator, which generates the field and current in the rotor to start the process. Then he can feed himself.
Asynchronous or synchronous motors
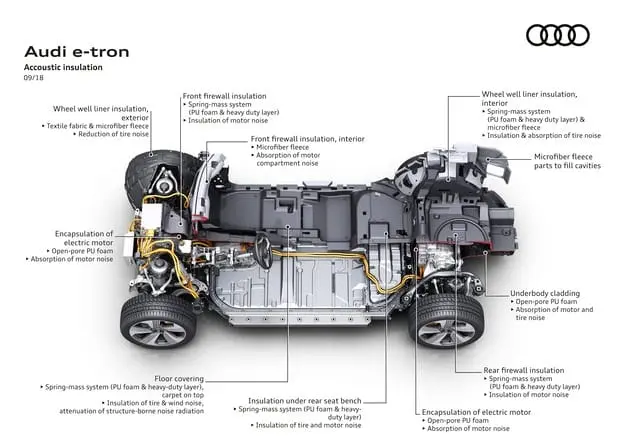
Synchronous blocks have significantly higher efficiency and power density. A significant difference between an induction motor is that the magnetic field in the rotor is not induced by interaction with the stator, but is the result of the current flowing through the additional windings installed in it, or permanent magnets. Thus, the field in the rotor and the field in the stator are synchronous, but the maximum motor speed also depends on the rotation of the field, respectively, on the current frequency and load. In order to avoid the need for additional power supply to the windings, which increases energy consumption and complicates current control, modern electric vehicles and hybrid models use electric motors with the so-called constant excitation, i.e. with permanent magnets. As already mentioned, almost all manufacturers of such cars currently use units of this type, therefore, according to many experts, there will still be a problem with a lack of expensive rare earth elements of neodymium and dysprosium. Reducing their use is part of the demand of engineers in this area.
The design of the rotor core gives the greatest potential for increasing the performance of an electric machine.
There are various technological solutions with surface-mounted magnets, disk-shaped rotor, with internally built-in magnets. Interesting here is Tesla's solution, which uses the aforementioned technology called Switched Reluctance Motor to drive the Model 3's rear axle. "Reluctance", or magnetic resistance, is a term opposite to magnetic conductivity, similar to electrical resistance and electrical conductivity of materials. Motors of this type use the phenomenon that magnetic flux tends to pass through the part of the material with the least magnetic resistance. As a result, it physically displaces the material it is flowing through in order to pass through the part with the least resistance. This effect is used in an electric motor to create a rotational movement - for this, materials with different magnetic resistance alternate in the rotor: hard (in the form of ferrite neodymium disks) and soft (steel disks). In an attempt to pass through lower resistance material, the magnetic flux from the stator rotates the rotor until it is positioned to do so. With current control, the field constantly rotates the rotor in a comfortable position. That is, the rotation is not initiated to such an extent by the interaction of the magnetic fields as the tendency of the field to flow through the material with the least resistance and the resultant effect of the rotation of the rotor. By alternating different materials, the number of expensive components is reduced.

Depending on the design, the efficiency curve and torque change with engine speed. Initially, the induction motor has the lowest efficiency, and the highest one has surface magnets, but in the latter it decreases sharply with speed. The BMW i3 engine has a unique hybrid character, thanks to a design that combines permanent magnets and the "reluctance" effect described above. Thus, the electric motor achieves the high levels of constant power and torque that are characteristic of machines with an electrically excited rotor, but has significantly less weight than them (the latter are efficient in many respects, but not in terms of weight). After all this, it's clear that efficiency is declining at high speeds, which is why more and more manufacturers are saying they'll focus on two-speed transmissions for electric motors.
Questions and answers:
What engines does Tesla use? All Tesla models are electric vehicles, so they are equipped exclusively with electric motors. Almost every model will have a 3-phase AC induction motor under the hood.
How does a Tesla engine work? An asynchronous electric motor works due to the occurrence of an EMF due to the rotation in a stationary stator of a magnetic field. Reverse travel is provided by polarity reversal on the starter coils.
Where is the Tesla engine located? Tesla cars are rear-wheel drive. Therefore, the motor is located between the rear axle shafts. The motor consists of a rotor and stator, which only contact each other via bearings.
How much does a Tesla engine weigh? The weight of the assembled electric motor for Tesla models is 240 kilograms. Basically one engine modification is used.
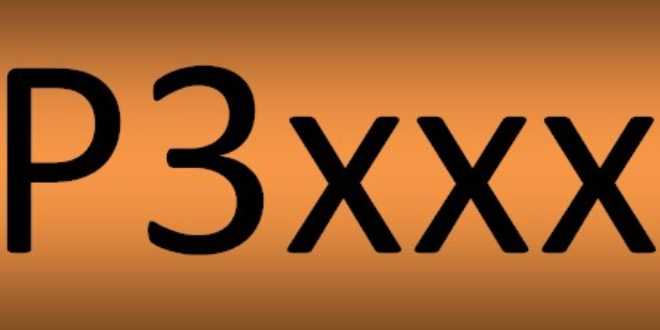
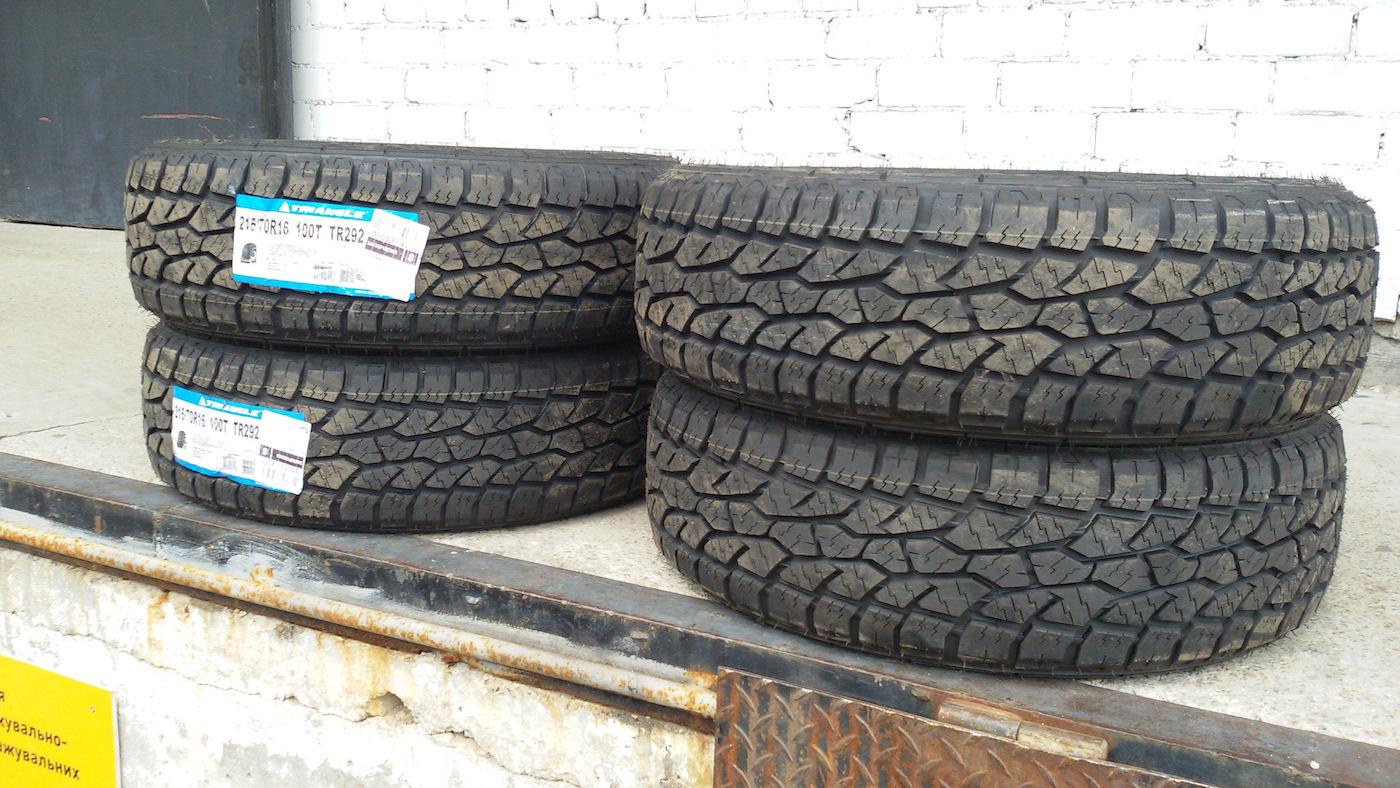
One comment
Jan Franzen
Error in the text Tesla should be the end of the 1800th century