
Probefahrt interne Reibung II
Schmierarten und Schmiermethode verschiedener Motorteile
Schmierarten
Die Wechselwirkungen von sich bewegenden Oberflächen, einschließlich Reibung, Schmierung und Verschleiß, sind das Ergebnis einer Wissenschaft namens Tribologie. Wenn es um die mit Verbrennungsmotoren verbundenen Reibungstypen geht, definieren Konstrukteure verschiedene Arten von Schmiermitteln. Die hydrodynamische Schmierung ist die am meisten nachgefragte Form dieses Prozesses, und der typische Ort, an dem sie auftritt, sind die Haupt- und Pleuellager der Kurbelwelle, die viel höheren Belastungen ausgesetzt sind. Es erscheint im Miniaturraum zwischen Lager und V-Welle und wird von einer Ölpumpe dorthin gebracht. Die bewegliche Oberfläche des Lagers wirkt dann als eigene Pumpe, die das Öl weiter pumpt und verteilt und schließlich einen ausreichend dicken Film über den gesamten Lagerraum erzeugt. Aus diesem Grund verwenden Konstrukteure Gleitlager für diese Motorkomponenten, da die minimale Kontaktfläche eines Kugellagers eine extrem hohe Belastung der Ölschicht erzeugt. Darüber hinaus kann der Druck in diesem Ölfilm fast fünfzigmal höher sein als der von der Pumpe selbst erzeugte Druck! In der Praxis werden die Kräfte in diesen Teilen durch die Ölschicht übertragen. Um den hydrodynamischen Schmierzustand aufrechtzuerhalten, ist es natürlich erforderlich, dass das Motorschmiersystem immer eine ausreichende Menge Öl bereitstellt.
Es ist möglich, dass der Schmierfilm unter dem Einfluss von Hochdruck in bestimmten Teilen irgendwann stabiler und härter wird als die zu schmierenden Metallteile und sogar zu einer Verformung der Metalloberflächen führt. Entwickler nennen diese Art der Schmierung elastohydrodynamisch und sie kann sich in den oben genannten Kugellagern, in Zahnrädern oder in Ventilstößeln manifestieren. Für den Fall, dass die Geschwindigkeit der beweglichen Teile relativ zueinander sehr niedrig wird, steigt die Last erheblich an oder es ist nicht genügend Öl vorhanden, was häufig zu einer sogenannten Grenzflächenschmierung führt. In diesem Fall hängt die Schmierung von der Haftung der Ölmoleküle an den Trägeroberflächen ab, so dass diese durch einen relativ dünnen, aber immer noch zugänglichen Ölfilm getrennt sind. Leider besteht in diesen Fällen immer die Gefahr, dass der Dünnfilm durch scharfe Teile von Unregelmäßigkeiten "durchstochen" wird. Daher werden den Ölen geeignete Verschleißschutzadditive zugesetzt, die das Metall für eine lange Zeit bedecken und dessen Zerstörung durch direkten Kontakt verhindern. Die hydrostatische Schmierung erfolgt in Form eines dünnen Films, wenn die Last abrupt die Richtung ändert und die Geschwindigkeit der beweglichen Teile sehr gering ist. Hier ist anzumerken, dass Lagerhersteller wie Hauptverbindungsstangen wie Federal-Mogul neue Technologien entwickelt haben, um sie zu beschichten, damit sie Probleme mit Start-Stopp-Systemen wie Lagerverschleiß bei häufigen, teilweise trockenen Starts lösen können dass sie bei jedem neuen Start ausgesetzt sind. Dies wird später besprochen. Diese häufige Inbetriebnahme führt wiederum zu einem Übergang von einer Schmiermittelform zu einer anderen und wird als „Mischfilmschmiermittel“ definiert.
Schmiersysteme
Die frühesten Automobil- und Motorrad-Verbrennungsmotoren und noch spätere Konstruktionen hatten eine Tropf-"Schmierung", bei der Öl von einer Art "automatischen" Schmiernippel durch die Schwerkraft in den Motor eindrang und nach dem Durchlaufen durchströmte oder ausbrannte. Konstrukteure definieren heute diese Schmiersysteme sowie Schmiersysteme für Zweitaktmotoren, bei denen Öl mit Kraftstoff vermischt wird, als "Totalverlustschmiersysteme". Später wurden diese Systeme durch Hinzufügen einer Ölpumpe verbessert, um das Innere des Motors und den (oft gefundenen) Ventiltrieb mit Öl zu versorgen. Diese Pumpsysteme haben jedoch nichts mit den späteren, heute noch gebräuchlichen Zwangsschmierungstechnologien zu tun. Die Pumpen wurden extern installiert und förderten das Öl in das Kurbelgehäuse, das dann durch Spritzen an die Reibungsteile gelangte. Spezielle Schaufeln im unteren Teil der Pleuel sprühten Öl in das Kurbelgehäuse und den Zylinderblock, wodurch überschüssiges Öl in Minibädern und Kanälen gesammelt wurde und unter Einwirkung der Schwerkraft in die Haupt- und Pleuellager floss und Nockenwellenlager. Eine Art Übergang zu Systemen mit Zwangsschmierung unter Druck ist der Ford-Modell-T-Motor, bei dem das Schwungrad so etwas wie ein Wassermühlenrad hatte, das Öl anheben und zum Kurbelgehäuse leiten sollte (und das Getriebe beachten), dann die unteren Teile Kurbelwelle und Pleuel kratzten Öl und bildeten ein Ölbad zum Reiben von Teilen. Dies war nicht besonders schwierig, da sich die Nockenwelle auch im Kurbelgehäuse befand und die Ventile stillstanden. Der Erste Weltkrieg und Flugmotoren, die in einem solchen Schmierstoff einfach nicht funktionierten, gaben einen starken Impuls in diese Richtung. So entstanden Systeme mit Innenpumpen und Mischdruck- und Sprühschmierung, die dann auf neue und höher belastete Automobilmotoren angewendet wurden.
Die Hauptkomponente dieses Systems war eine motorgetriebene Ölpumpe, die Öl unter Druck nur zu den Hauptlagern pumpte, während andere Teile auf Sprühschmierung beruhten. Daher war es nicht erforderlich, Nuten in der Kurbelwelle zu bilden, die für Systeme mit vollständig erzwungener Schmierung erforderlich sind. Letzteres entstand als Notwendigkeit bei der Entwicklung von Motoren, die Geschwindigkeit und Last erhöhen. Dies bedeutete auch, dass die Lager nicht nur geschmiert, sondern auch gekühlt werden mussten.
In diesen Systemen werden die Haupt- und unteren Pleuellager (letztere erhalten Öl durch Nuten in der Kurbelwelle) und die Nockenwellenlager mit Drucköl versorgt. Der große Vorteil dieser Systeme besteht darin, dass Öl praktisch durch diese Lager zirkuliert, d.h. geht durch sie hindurch und tritt in das Kurbelgehäuse ein. Dadurch liefert das System viel mehr Öl als für die Schmierung notwendig ist und wird daher intensiv gekühlt. Bereits in den 60er Jahren führte beispielsweise Harry Ricardo erstmals eine Regel ein, die den Umlauf von drei Litern Öl pro Stunde vorsah, also für einen 3-PS-Motor. – XNUMX Liter Ölumlauf pro Minute. Heutige Fahrräder werden um ein Vielfaches nachgebaut.
Die Ölzirkulation im Schmiersystem umfasst ein Netzwerk von Kanälen, die in die Karosserie und den Motormechanismus eingebaut sind und deren Komplexität von der Anzahl und Position der Zylinder und dem Zeitsteuerungsmechanismus abhängt. Aus Gründen der Zuverlässigkeit und Langlebigkeit des Motors bevorzugen Konstrukteure seit langem kanalförmige Kanäle anstelle von Rohrleitungen.
Eine motorgetriebene Pumpe saugt Öl aus dem Kurbelgehäuse an und leitet es zu einem Inline-Filter, der außerhalb des Gehäuses montiert ist. Es dauert dann einen (für Reihen-) oder zwei Kanäle (für Boxer- oder V-förmige Motoren), die sich fast über die gesamte Länge des Motors erstrecken. Dann wird es unter Verwendung kleiner Quernuten auf die Hauptlager gerichtet und tritt durch den Einlass in der oberen Lagerschale in diese ein. Durch einen Umfangsschlitz im Lager wird ein Teil des Öls zur Kühlung und Schmierung gleichmäßig im Lager verteilt, während der andere Teil durch eine schräge Bohrung in der Kurbelwelle, die mit demselben Schlitz verbunden ist, zum unteren Pleuellager geleitet wird. Das Schmieren des oberen Pleuellagers ist in der Praxis schwieriger, so dass der obere Teil der Pleuelstange häufig ein Reservoir ist, das Ölspritzer unter dem Kolben enthält. In einigen Systemen gelangt Öl durch eine Bohrung in der Pleuelstange selbst zum Lager. Die Kolbenbolzenlager sind wiederum sprühgeschmiert.
Ähnlich dem Kreislaufsystem
Wenn ein Nockenwellen- oder Kettenantrieb in das Kurbelgehäuse eingebaut ist, wird dieser Antrieb mit Direktöl geschmiert, und wenn die Welle in den Kopf eingebaut ist, wird die Antriebskette durch kontrollierte Ölleckage aus dem hydraulischen Verlängerungssystem geschmiert. Beim Ford 1.0 Ecoboost Motor wird auch der Antriebsriemen der Nockenwelle geschmiert – in diesem Fall durch Eintauchen in die Ölwanne. Die Art und Weise, wie Schmieröl den Nockenwellenlagern zugeführt wird, hängt davon ab, ob der Motor eine untere oder obere Welle hat – erstere erhält sie normalerweise genutet von den Hauptlagern der Kurbelwelle und letztere genutet mit der unteren Hauptnut verbunden. oder indirekt, mit einem separaten gemeinsamen Kanal im Kopf oder in der Nockenwelle selbst, und wenn zwei Wellen vorhanden sind, wird dies mit zwei multipliziert.
Konstrukteure sind bestrebt, Systeme zu entwickeln, in denen Ventile mit genau gesteuerten Durchflussraten geschmiert werden, um ein Überfluten und ein Austreten von Öl durch die Ventilführungen in den Zylindern zu vermeiden. Zusätzliche Komplexität wird durch das Vorhandensein von hydraulischen Aufzügen hinzugefügt. Steine, Unregelmäßigkeiten werden in einem Ölbad oder durch Sprühen in Miniaturbädern oder durch Kanäle, durch die Öl den Hauptkanal verlässt, geschmiert.
Die zylindrischen Wände und Kolbenschürzen sind ganz oder teilweise mit Öl geschmiert, das aus den unteren Pleuellagern im Kurbelgehäuse austritt und sich dort ausbreitet. Kürzere Motoren sind so konstruiert, dass ihre Zylinder mehr Öl aus dieser Quelle beziehen, da sie einen größeren Durchmesser haben und näher an der Kurbelwelle liegen. Bei einigen Motoren ziehen die Zylinderwände zusätzliches Öl aus einem Seitenloch im Pleuelgehäuse, das normalerweise auf die Seite gerichtet ist, auf der der Kolben mehr seitlichen Druck auf den Zylinder ausübt (auf den der Kolben während der Verbrennung während des Betriebs Druck ausübt). ... Bei V-förmigen Motoren ist es üblich, Öl von einer Pleuelstange, die sich in den gegenüberliegenden Zylinder bewegt, auf die Zylinderwand einzuspritzen, so dass die Oberseite geschmiert und dann zur Unterseite gezogen wird. Hierbei ist zu beachten, dass bei Turbomotoren Öl über den Hauptölkanal und die Rohrleitung in dessen Lager gelangt. Sie verwenden jedoch häufig einen zweiten Kanal, der den Ölfluss zu speziellen Düsen leitet, die auf die Kolben gerichtet sind und diese kühlen sollen. In diesen Fällen ist die Ölpumpe viel leistungsstärker.
In Trockensumpfsystemen nimmt die Ölpumpe Öl aus einem separaten Öltank auf und verteilt es auf die gleiche Weise. Die Hilfspumpe saugt das Öl / Luft-Gemisch aus dem Kurbelgehäuse (daher muss es eine große Kapazität haben), das durch das Gerät fließt, um dieses zu trennen und in den Vorratsbehälter zurückzuführen.
Das Schmiersystem kann auch einen Kühler zum Kühlen des Öls in schwereren Motoren (dies war bei älteren Motoren mit einfachen Mineralölen üblich) oder einen an das Kühlsystem angeschlossenen Wärmetauscher enthalten. Dies wird später besprochen.
Ölpumpen und Überdruckventile
Ölpumpen inklusive Zahnradpaar eignen sich hervorragend für den Betrieb eines Ölsystems und sind daher in Schmiersystemen weit verbreitet und werden in den meisten Fällen direkt von der Kurbelwelle angetrieben. Eine weitere Option sind Kreiselpumpen. Neuerdings kommen auch Flügelzellenpumpen zum Einsatz, darunter auch Verstellversionen, die den Betrieb und damit ihre Leistung in Bezug auf die Drehzahl optimieren und den Energieverbrauch senken.
Ölsysteme erfordern Überdruckventile, da bei hohen Drehzahlen die Erhöhung der von der Ölpumpe gelieferten Menge nicht mit der Menge übereinstimmt, die durch die Lager fließen kann. Dies liegt an der Tatsache, dass in diesen Fällen starke Zentrifugalkräfte im Lageröl gebildet werden, die die Zufuhr einer neuen Ölmenge zum Lager verhindern. Darüber hinaus erhöht das Starten des Motors bei niedrigen Außentemperaturen die Ölbeständigkeit mit einer Zunahme der Viskosität und einer Abnahme des Spiels der Mechanismen, was häufig zu kritischen Werten des Öldrucks führt. Die meisten Sportwagen verwenden einen Öldrucksensor und einen Öltemperatursensor.
(Folgen)
Text: Georgy Kolev
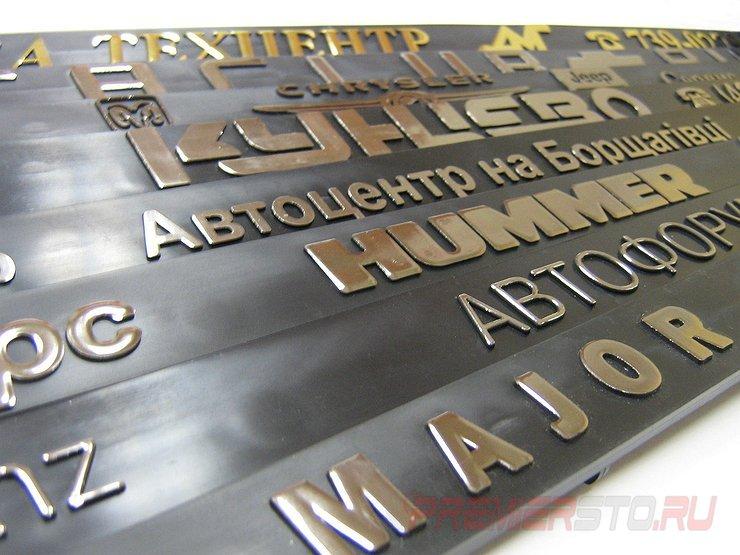
