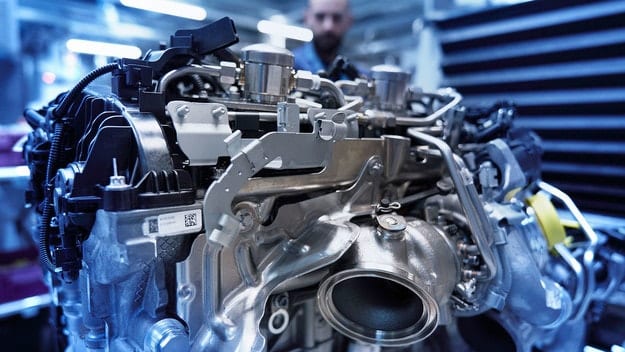
Nockenwellenmodul: Kunststoff statt Metall
Inhalt
Das neue Produkt verspricht Vorteile in Bezug auf Gewicht, Kosten und Ökologie
Forscher des Fraunhofer-Instituts haben gemeinsam mit Experten von Mahle und Daimler ein neues Material für Gehäuse entwickelt, in die Nockenwellen eingebaut sind. Experten zufolge wird dies viele Vorteile bringen.
Wer hat gesagt, dass die Tage eines Verbrennungsmotors gezählt sind? Wenn Sie nachverfolgen, wie viele Innovationen für die klassische Bewegungsform weiterentwickelt werden, werden Sie leicht feststellen, dass diese konstante These übertrieben ist, wenn nicht falsch gesagt. Forschungsgruppen führen ständig neue Lösungen ein, die Benzin-, Diesel- und Gasmotoren leistungsfähiger, wirtschaftlicher und oft gleichzeitig machen.
Verstärkt mit Kunstharz anstelle von Aluminium.
Genau das tun Wissenschaftler des Fraunhofer-Instituts für Chemische Technologie (IKT). Gemeinsam mit Spezialisten von Daimler, Mahle und anderen Zulieferern von Bauteilen für die Automobilindustrie entwickelten sie einen neuartigen Nockenwellenmodul, der eher aus Kunststoff als aus Leichtmetall besteht. Das Modul ist ein wichtiger Bestandteil des Antriebspfads, daher ist Stabilität die wichtigste Voraussetzung für Konstrukteure. Fraunhofer-Spezialisten verwenden jedoch ein hochfestes wärmehärtbares Polymer (Kunstharze), faserverstärkt, anstelle von Aluminium als Material für das Modul, das als Nockenwellengehäuse dient.
Die Autoren der Entwicklung behaupten, dass dies mehrere Vorteile gleichzeitig bringen wird. Einerseits in Bezug auf das Gewicht: „Das Nockenwellenmodul befindet sich im Zylinderkopf, also normalerweise oben auf dem Antriebsweg“, erklärt Thomas Sorg, Wissenschaftler am Fraunhofer-Institut. Hier ist eine Gewichtsersparnis besonders ratsam, da Sie so den Schwerpunkt des Autos verringern können. " Das ist aber nicht nur gut für die Dynamik der Straße. Gewichtsverlust ist letztendlich eine der effektivsten Methoden zur Reduzierung der CO2-Emissionen von Autos.
Kosten- und Klimavorteile
Obwohl das am Institut entwickelte Teil leichter ist als das Aluminium-Nockenwellenmodul, behaupten seine Hersteller, dass es extrem widerstandsfähig gegen hohe Temperaturen und mechanische und chemische Belastungen ist, die beispielsweise durch synthetische Motorenöle und Kühlmittel verursacht werden. Akustisch hat die Neuentwicklung auch Vorteile. Da sich Kunststoffe wie Schalldämmer verhalten, „kann das akustische Verhalten des Nockenwellenmoduls sehr gut optimiert werden“, erklärt Sorg.
Der größte Vorteil können jedoch niedrige Kosten sein. Nach dem Gießen müssen Aluminiumteile eine teure Oberfläche erhalten und ihre Lebensdauer ist begrenzt. Zum Vergleich sind die Kosten für die zusätzliche Verarbeitung von faserverstärkten duroplastischen Materialien relativ gering. Dank ihres monolithischen Designs können Sie das Teil im Werk vorbearbeiten, wo es mit nur wenigen Handbewegungen am Motor installiert werden kann. Darüber hinaus verspricht das Fraunhofer ICT eine deutlich längere Lebensdauer für seine Neuentwicklung.
Letztendlich wird es auch Klimavorteile geben. Da die Aluminiumproduktion viel Energie verbraucht, sollte der COXNUMX-Fußabdruck des Glasfaser-Nockenwellenmoduls des Durometers erheblich geringer sein.
Abschluss
Derzeit das Nockenwellenmodul des Instituts für ICT. Noch befindet sich Fraunhofer im Stadium eines funktionierenden Demonstrationsmodells. Auf dem Motorprüfstand wurde das Teil 600 Stunden getestet. „Wir sind sehr zufrieden mit dem funktionierenden Prototyp und den Testergebnissen“, sagte Catherine Schindele, Projektleiterin bei Mahle. Allerdings haben sich die Partner bislang nicht mit der Frage auseinandergesetzt, unter welchen Bedingungen eine Serienanwendung der Entwicklung geplant werden kann.

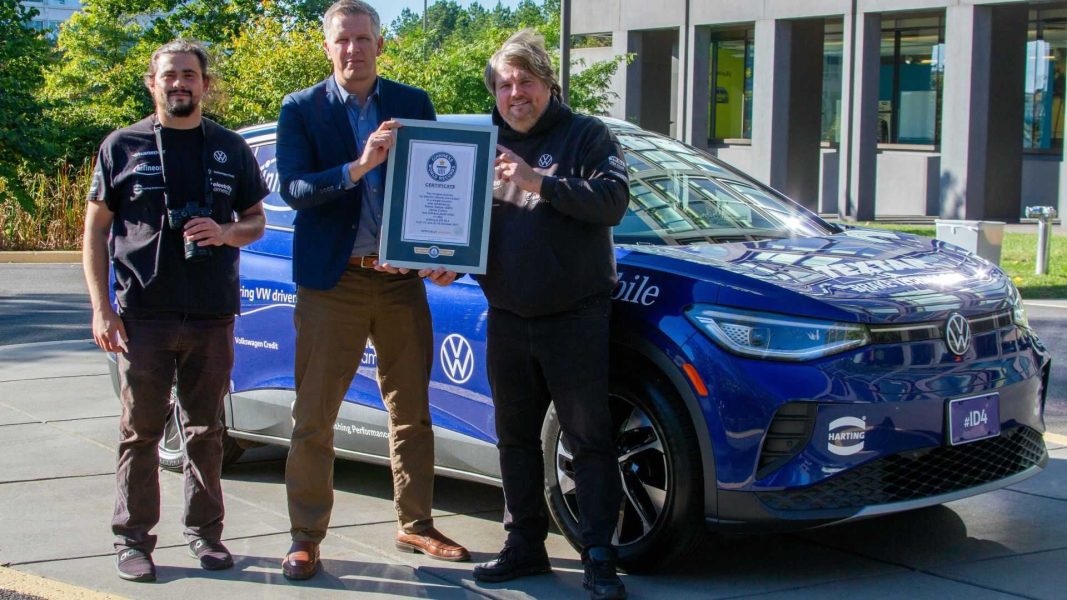