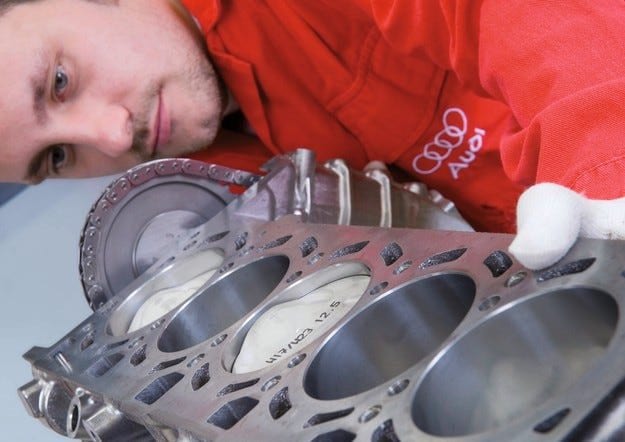
Probefahrt Audi Motorenprogramm - Teil 1: 1.8 TFSI
Das Antriebssortiment der Marke ist der Inbegriff unglaublicher Hightech-Lösungen.
Eine Serie über die interessantesten Autos des Unternehmens
Wenn wir nach einem Beispiel für eine zukunftsweisende Wirtschaftsstrategie suchen, die eine nachhaltige Entwicklung des Unternehmens sicherstellt, dann kann Audi hier ein hervorragendes Beispiel sein. Kaum jemand hätte sich in den 70er Jahren vorstellen können, dass das Unternehmen aus Ingolstadt heute einem so etablierten Namen wie Mercedes-Benz ebenbürtig sein wird. Die Antwort auf die Gründe findet sich maßgeblich im Markenslogan „Fortschritt durch Technologien“, der die Basis für den erfolgreich bewältigten schwierigen Weg ins Premiumsegment bildet. Ein Bereich, in dem niemand das Recht hat, Kompromisse einzugehen und nur das Beste bietet. Was Audi und nur eine Handvoll anderer Unternehmen leisten können, garantiert ihnen die Nachfrage nach ihren Produkten und das Erreichen ähnlicher Parameter, aber auch eine enorme Belastung, die ständige Bewegung am Rande eines technologischen Rasiermessers erfordert.
Als Teil des VW-Konzerns hat Audi die Möglichkeit, die Entwicklungsmöglichkeiten eines riesigen Unternehmens voll auszuschöpfen. Was auch immer VW für Probleme hat, mit seinen jährlichen F&E-Ausgaben von fast 10 Milliarden Euro führt der Konzern die Liste der 50 am höchsten investierten Unternehmen in diesem Bereich an, vor Giganten wie Samsung Electronics, Microsoft, Intel und Toyota (wo dieser Wert sich beläuft knapp über 7 Milliarden Euro). Alleine Audi liegt in diesen Parametern nahe an BMW mit einer Investition von 4,0 Milliarden Euro. Ein Teil der in Audi investierten Mittel stammt jedoch indirekt aus der allgemeinen Kasse des VW-Konzerns, da die Entwicklungen auch von anderen Marken genutzt werden. Zu den Schwerpunkten dieser Tätigkeit gehören Technologien zur Herstellung von Leichtbaustrukturen, Elektronik, Getrieben und natürlich Antrieben. Und jetzt kommen wir zur Essenz dieses Materials, das Teil unserer Serie ist und moderne Lösungen im Bereich der Verbrennungsmotoren darstellt. Als Elite-Division von VW entwickelt Audi jedoch auch eine bestimmte Antriebsstranglinie, die hauptsächlich oder ausschließlich für Audi-Fahrzeuge entwickelt wurde und über die wir Sie hier informieren.
1.8 TFSI: In jeder Hinsicht ein Modell der Hochtechnologie
Die Geschichte von Audi mit vier Reihen-TFSI-Motoren reicht bis Mitte 2004 zurück, als der weltweit erste Benzin-Turbolader EA113 mit Direkteinspritzung als 2.0 TFSI veröffentlicht wurde. Zwei Jahre später erschien eine leistungsstärkere Version des Audi S3. Die Entwicklung des modularen Konzepts EA888 mit Nockenwellenantrieb und Kette begann praktisch 2003, kurz vor der Einführung des EA113 mit Zahnriemen.
Der EA888 wurde jedoch von Grund auf als globaler Motor für den VW-Konzern gebaut. Die erste Generation wurde 2007 eingeführt (als 1.8 TFSI und 2.0 TFSI); Mit der Einführung der variablen Ventilsteuerung Audi Valvelift und einer Reihe von Maßnahmen zur Reduzierung der inneren Reibung wurde 2009 die zweite Generation vermerkt, Ende 2011 folgte die dritte Generation (1.8 TFSI und 2.0 TFSI). Die Vierzylinder-Baureihen EA113 und EA888 haben für Audi einen unglaublichen Erfolg erzielt und insgesamt zehn prestigeträchtige Auszeichnungen als „International Engine of the Year“ und „10 Best Engines“ gewonnen. Die Aufgabe der Ingenieure besteht darin, einen modularen Motor mit 1,8 und 2,0 Liter Hubraum zu schaffen, der sowohl für den Quer- als auch für den Längseinbau geeignet ist, mit deutlich reduzierter innerer Reibung und Emissionen, neue Anforderungen, einschließlich Euro 6, mit verbesserter Leistung erfüllt. Ausdauer und reduziertes Gewicht. Basierend auf dem EA888 Generation 3 wurde im vergangenen Jahr der EA888 Generation 3B entwickelt und eingeführt, der nach einem ähnlichen Prinzip wie das Miller-Prinzip arbeitet. Wir werden später darüber sprechen.
Das klingt alles gut, aber wie wir sehen werden, ist eine Menge Entwicklungsarbeit erforderlich, um dies zu erreichen. Dank des im Vergleich zum 250-Liter-Vorgänger von 320 auf 1,8 Nm gesteigerten Drehmoments können Konstrukteure jetzt in längere Übersetzungen wechseln, was ebenfalls den Kraftstoffverbrauch senkt. Zu letzterem hat eine wichtige technologische Lösung einen großen Beitrag geleistet, die dann von einer Reihe anderer Unternehmen genutzt wurde. Dies sind in den Kopf integrierte Auspuffrohre, die die Möglichkeit bieten, die Betriebstemperatur schnell zu erreichen und Gase unter hoher Last zu kühlen und die Notwendigkeit einer Anreicherung des Gemischs zu vermeiden. Eine solche Lösung ist äußerst rationell, aber angesichts der großen Temperaturunterschiede zwischen den Flüssigkeiten auf beiden Seiten der Sammelrohre auch sehr schwierig umzusetzen. Zu den Vorteilen zählen aber auch die Möglichkeit einer kompakteren Bauweise, die neben der Gewichtsreduzierung einen kürzeren und optimaleren Gasweg zur Turbine und ein kompakteres Modul zur Zwangsbefüllung und Kühlung von Druckluft garantiert. Theoretisch klingt das auch originell, aber die praktische Umsetzung ist eine echte Herausforderung für Casting-Profis. Um einen komplexen Zylinderkopf zu gießen, schaffen sie ein spezielles Verfahren mit bis zu 12 metallurgischen Herzen.
Flexible Kühlsteuerung
Ein weiterer wichtiger Faktor zur Reduzierung des Kraftstoffverbrauchs ist der Prozess des Erreichens der Betriebstemperatur des Kühlmittels. Das intelligente Steuerungssystem des letzteren ermöglicht es ihm, seine Zirkulation vollständig zu stoppen, bis es die Betriebstemperatur erreicht, und wenn dies geschieht, wird die Temperatur abhängig von der Motorlast ständig überwacht. Die Planung eines Bereichs, in dem Kühlmittel die Auspuffrohre überflutet und in dem ein erheblicher Temperaturgradient besteht, war eine große Herausforderung. Zu diesem Zweck wurde ein komplexes analytisches Computermodell entwickelt, das die Gesamtzusammensetzung des Gases / Aluminiums / Kühlmittels enthält. Aufgrund der Besonderheit einer starken lokalen Erwärmung der Flüssigkeit in diesem Bereich und der allgemeinen Notwendigkeit einer optimalen Temperaturregelung wird ein Polymerrotor-Steuermodul verwendet, das den herkömmlichen Thermostat ersetzt. Somit ist in der Heizphase die Zirkulation des Kühlmittels vollständig blockiert.
Alle externen Ventile sind geschlossen und das Wasser im Mantel gefriert. Auch wenn die Kabine bei kaltem Wetter beheizt werden muss, wird die Zirkulation nicht aktiviert, sondern es kommt eine spezielle Schaltung mit einer zusätzlichen Elektropumpe zum Einsatz, bei der die Abgaskrümmer umströmt werden. Mit dieser Lösung können Sie viel schneller eine angenehme Temperatur in der Kabine bereitstellen und gleichzeitig die Fähigkeit bewahren, den Motor schnell aufzuwärmen. Wenn das entsprechende Ventil geöffnet wird, beginnt eine intensive Flüssigkeitszirkulation im Motor - so schnell wird die Betriebstemperatur des Öls erreicht, wonach sich das Ventil seines Kühlers öffnet. Die Kühlmitteltemperatur wird je nach Last und Geschwindigkeit in Echtzeit überwacht und reicht von 85 bis 107 Grad (am höchsten bei niedriger Geschwindigkeit und Last) im Namen eines Gleichgewichts zwischen Reibungsreduzierung und Klopfverhinderung. Und das ist noch nicht alles – auch wenn der Motor ausgeschaltet ist, zirkuliert eine spezielle elektrische Pumpe das Kühlmittel weiter durch das kochempfindliche Hemd in Kopf und Turbolader, um ihnen schnell Wärme zu entziehen. Letzteres wirkt sich nicht auf die Oberteile von Hemden aus, um deren schnelle Unterkühlung zu vermeiden.
Zwei Düsen pro Zylinder
Speziell für diesen Motor führt Audi zum Erreichen der Abgasstufe Euro 6 erstmals ein Einspritzsystem mit zwei Düsen pro Zylinder ein – eine für die Direkteinspritzung und die andere für das Saugrohr. Die Möglichkeit, die Einspritzung jederzeit flexibel zu steuern, führt zu einer besseren Durchmischung von Kraftstoff und Luft und reduziert die Partikelemissionen. Der Druck in der Direkteinspritzung wurde von 150 auf 200 bar erhöht. Wenn letzterer nicht läuft, wird Kraftstoff auch über Bypass-Verbindungen durch Injektoren in den Saugrohren zirkuliert, um die Hochdruckpumpe zu kühlen.
Beim Starten des Motors wird das Gemisch vom Direkteinspritzsystem aufgenommen und eine Doppeleinspritzung durchgeführt, um ein schnelles Erhitzen des Katalysators sicherzustellen. Diese Strategie bietet ein besseres Mischen bei niedrigen Temperaturen, ohne die kalten Metallteile des Motors zu überfluten. Gleiches gilt für schwere Lasten, um eine Detonation zu vermeiden. Dank des Abgaskrümmer-Kühlsystems und seiner kompakten Bauweise kann ein Einstrahl-Turbolader (RHF4 von IHI) mit einer Lambda-Sonde davor und einem Gehäuse aus billigeren Materialien verwendet werden.
Dies ergibt ein maximales Drehmoment von 320 Nm bei 1400 U / min. Noch interessanter ist die Leistungsverteilung mit einem Maximalwert von 160 PS. ist bei 3800 U / min (!) verfügbar und bleibt auf diesem Niveau bis zu 6200 U / min mit erheblichem Potenzial für eine weitere Erhöhung (wodurch verschiedene Versionen des 2.0 TFSI installiert werden, wodurch das Drehmoment in hohen Bereichen erhöht wird). Die Leistungssteigerung gegenüber dem Vorgänger (um 12 Prozent) geht somit mit einer Verringerung des Kraftstoffverbrauchs (um 22 Prozent) einher.
(Folgen)
Text: Georgy Kolev
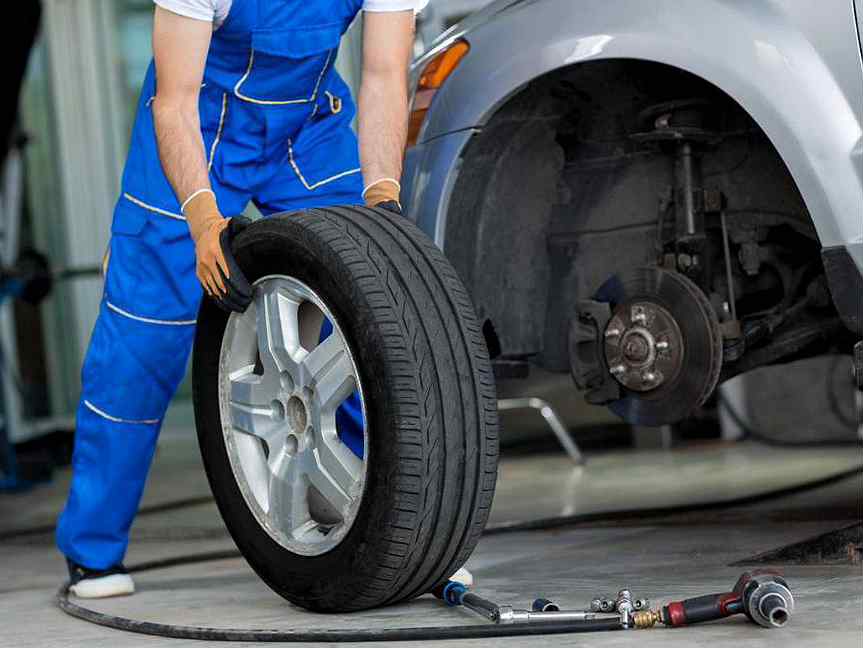
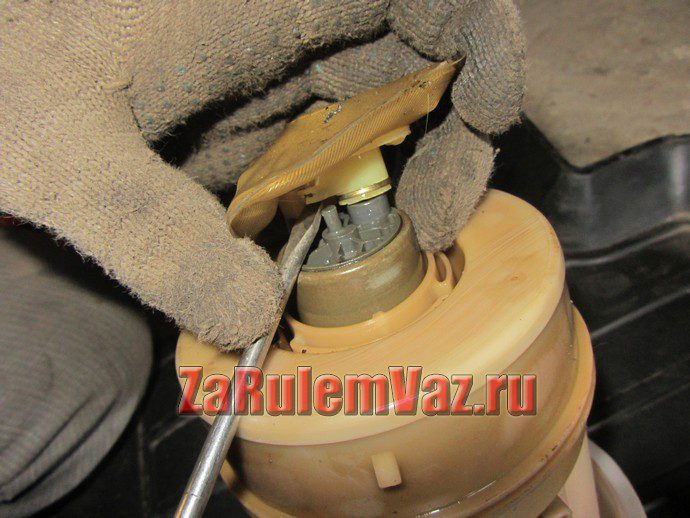